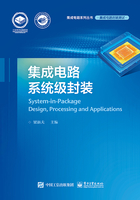
3.2.5 可靠性设计
电子封装产品的制造环境和使用环境比较复杂。环境在发生变化时,封装产品会产生一些可靠性问题,如分层、基板翘曲、球脱、键合开裂、凸点开裂(Bump Crack)、芯片开裂(Die Crack)、焊锡空洞(SMT Void)、塑封料包封不良与空洞等。封装的可靠性设计是指在设计初期把可能出现的失效问题通过设计手段进行相应风险的降低或规避,通常在结构、材料、工艺、产品的电性能、散热性、应力方面进行设计优化,以下对可靠性的设计主要围绕常用结构优化设计进行。
常见的可靠性失效模式及对应的结构设计优化如下。
1. 分层
环氧树脂塑封料及有机基板逐渐取代了陶瓷封装和金属封装,成了目前封装的主流形式。这些有机材料吸湿率较高,当在生产和可靠性试验中经历高温和高湿环境时,湿气进入封装体,材料膨胀,内部应力增加,导致分层,如图3-62所示。

图3-62 分层形成的示意图
分层又称剥离,主要是指不同物质在接触面产生分离和缝隙,空气、水或酸碱液进入,导致电性能失效或产生失效隐患的现象。
根据分层的原因不同,分层失效模式主要分为以下两类。
第一类是塑封料内部存在湿气。塑封料的原材料存储、成品生产及成品存储都难免会接触到湿气,以及存在塑封料醒料环境不达标等情况,因而塑封料内部会聚集湿气,在进行后固化、可靠性试验、回流等一系列高温环境下的处理时,水气化导致塑封料体积迅速膨胀上千倍,进而导致分层。
第二类是半导体封装材料热膨胀系数差异过大。塑封料、芯片、框架等材质不同,热膨胀系数不同,因此接触面在高温下出现剪切应力。如果剪切应力过大,则容易出现分层。引起界面分层的主要原因是不同材料的热膨胀系数不同,以及界面结合力差。
封装中出现界面分层的情况大致可以分为以下三类。
(1)镀金面与塑封料分层。
一般出现这种类型的分层有以下几个因素。
• 镀金层表面附着有机物质,导致镀金区域与塑封料分层。
• 异质材料彼此间热膨胀系数差异太大,回流焊接时因高低温的膨胀与收缩而分层。
• 镀金层表面粗糙度不足,过于光滑,塑封料锁不住镀金层,从而分层。
• 在塑封过程中,模温过低或塑封料过期致使塑封料的黏性下降,从而分层。
• 在塑封过程中,塑封的压力不足,塑封料的密度不足,锁不住镀金层,从而分层。
图3-63所示为镀金面与塑封料分层示例。
引线键合的镀金区域称为金手指,为规避上述风险,设计时会在大片金手指区域增加分隔槽,槽区域内采用绿漆开口,但不覆铜镀金;或者增加绿漆覆盖面积,使塑封料与基板材料或绿漆结合,增大界面的结合力。金手指区域增加分隔槽,如图3-64所示。

图3-63 镀金面与塑封料分层示例

图3-64 金手指区域增加分隔槽
(2)镀金区与装片胶(Die Attach Adhesive)分层。
在一些产品中,为了满足散热和导电要求,会把芯片通过导电胶黏接在载板上裸露的镀金区域,这种大面积的镀金区域与装片胶的界面也会因为应力等因素出现分层现象,如图3-65所示。

图3-65 镀金区域与装片胶分层示例
(3)绿漆与铜界面分层。
整片的大块铜界面与绿漆结合的位置也经常出现分层。产生这种分层现象的原因包括界面之间外来物污染、环境湿度过大、系列温度变化。为了改善这一现象,在进行基板设计时,将需要大片覆铜的区域设置为网格覆铜,使部分绿漆与基板材料直接结合,增大界面的结合力,如图3-66所示。
2. 基板翘曲
系统级封装采用多种不同材料,如芯材、基板材料、塑封料等。这些材料的杨氏模量及热膨胀系数各不相同。当温度发生变化时,各个材料收缩或膨胀,材料间热膨胀系数的差异会使封装体翘曲。例如,在冷却过程中,如果上表面收缩得少,下表面收缩得多,则封装体向下翘曲;在加热过程中,如果上表面膨胀得少,下表面膨胀得多,则封装体向上翘曲,如图3-67所示。

图3-66 大片覆铜区域的网格覆铜示意图

图3-67 翘曲示意图
封装翘曲值是指平面度的偏差,封装底部平面相对于基准面的最高点与最低点的差值即封装翘曲值,如图3-68所示。

图3-68 封装翘曲值的定义
封装翘曲值定义如下。
翘曲为正值表示翘曲形态为凸起,即哭脸翘曲。
翘曲为负值表示翘曲形态为凹陷,即笑脸翘曲。
封装体翘曲会引起一系列可靠性问题,如分层、芯片开裂、焊点疲劳、表面贴装锡开路、切割及植球对位困难。
基板通常由绿漆、铜、半固化片、芯材等组成,各层材料的分布不均及热膨胀系数不同,在封装过程中,当温度发生变化时基板会明显翘曲,如图3-69所示。

图3-69 基板明显翘曲示意图
在设计基板叠层结构时,根据基板厚度、芯片厚度、封装尺寸等综合评估,选择热膨胀系数较低的芯材和半固化片,并匹配异质材料的热应力情况,降低基板翘曲的风险。另外,在设计基板时,也可以通过控制相对层的残铜率及残墨率来降低翘曲程度,具体改善方法如下。
(1)基板正面和背面残铜比差值(A)≤10%。
(2)基板正面和背面残墨比差值(B)≤15%。
(3)A与B的差值(GAP)≤10%。
(4)相同线路层单个残铜比与整条(Strip)残铜比差值≤10%。
3. 球脱和键合开裂
造成球脱和键合开裂的原因有很多:在正向引线键合时,第一焊点在芯片焊盘上形成焊球,第二焊点在基板上形成鱼尾,在回流焊接过程中,如果受到塑封料膨胀的异常应力,第一焊点可能球脱;在反向引线键合时,先在芯片焊盘上种植焊球;第一焊点在基板上形成焊球;第二焊点在芯片的焊球上形成鱼尾焊球,在回流焊接过程中,塑封料和芯片受热膨胀产生的应力不同,轻则球边缘轻微开裂,重则分层球脱,进而互连开路。球脱和正常键合的对比图如图3-70所示。

图3-70 球脱和正常键合的对比图
背面绿漆开口边缘区域是产生键合开裂的高风险区域。此区域受到塑封工艺的压力影响相对较大,容易出现焊球键合的受力不均衡,正面可能产生键合开裂的风险也最高。在设计时,基板上金手指尽量远离此高风险区域。焊点位置设计示意图如图3-71所示。
4. 凸点开裂
在倒装工艺中,凸点开裂是一种常见的失效模式,产生的原因也很多。例如,包封工序所采用的塑封材料由于热膨胀系数存在差异,因此应力分布不均匀,从而引起凸点与焊盘的开裂。凸点开裂截面图如图3-72所示。

图3-71 焊点位置设计示意图

图3-72 凸点开裂截面图
随着半导体芯片中晶体管尺寸越来越小,功能越来越多,倒装芯片技术为了匹配这种不断增加的连接密度,凸点间距持续不断地减小。锡球凸点由于自身尺寸的缩小达到其技术瓶颈,因此无法满足更小的凸点间距要求,而铜柱凸点有效满足了凸点间距减小的需求。铜柱凸点上电镀有焊锡,使其可以在小间距下保证可靠的焊接键合,实现高密度互连,同时提升电性能及散热性能。铜柱凸点外形图如图3-73所示。

图3-73 铜柱凸点外形图
相比传统的锡球材料,铜柱材料具有高杨氏模量和刚度,机械损伤风险较大,特别是在倒装芯片装片过程中可能引起低介电常数层的结构损伤。在倒装芯片装片回流过程中,无铅焊料在220℃左右凝结与基板实现固定连接。基板材料的热膨胀系数较大(CTE=16×10-6℃),硅芯片材料的热膨胀系数较小(CTE=2.8×10-6℃),在温度从220℃下降到室温过程中,基板较大程度的收缩会产生哭脸翘曲。铜柱与芯片的结合处产生应力差异,特别是在芯片角上的凸点应力较大,导致凸点开裂,如图3-74所示。

图3-74 凸点开裂示意图
焊点可靠性一直是封装行业中关键的可靠性问题之一。焊点既大部分是封装结构中比较脆弱的地方,又是封装互连中重要的一环,所以对焊点的失效分析尤为重要。系统级封装在进行热循环可靠性试验时,随着温度变化,封装体和PCB会因热膨胀系数不匹配产生不同比例的膨胀或收缩,介于封装体和PCB中间的焊点会因此承受不同方向及大小的应力,从而开裂。在进行跌落试验时,PCB和封装体在外场作用下的冲击形变或振动会传递到互连的焊点上,导致焊点开裂,如图3-75所示。

图3-75 焊点开裂示意图
在前期设计过程中,要改善凸点开裂现象,可以通过减小塑封料应力及加固凸点等方式来实现,具体方法如下。
(1)基板背面的基岛大面积铜区域绿漆避免出现大尺寸单一开窗,可按宫格方式设计成多个小开口的基岛,减小封装工艺过程中的变形,缓解基岛区域的应力,如图3-76所示。
(2)在放置倒装芯片时,避免将其放于背面绿漆开口边缘,此区域为应力最大区域,开口边缘长度最好在200μm以上,如图3-77所示。

图3-76 基岛宫格设计示意图
(3)适当增大凸点尺寸及增加凸点数量,并使凸点排布更加均匀一致,以改善局部应力过大的状况,如图3-78所示。

图3-77 倒装芯片位置示意图

图3-78 凸点分布示意图
5. 芯片开裂
结构与材料选择不当或外部环境导致的热变形过大、局部集中应力过大等会导致芯片开裂,如结构布局不合理有可能产生局部应力过于集中的情况,设计时应尽可能避免“不建议”的设计示例,将其优化成好的设计示例,如图3-79所示。
6. 焊锡空洞
业内通常要求焊锡空洞率≤30%。造成焊锡空洞率过大的原因有多种,与焊锡材料、钢网开口与厚度、回流曲线等因素有关,这里主要讨论结构设计优化,其他因素与优化措施在后续章节中介绍。在系统级封装的设计过程中,LGA基岛面积过大极易产生焊锡空洞风险,出于可靠性的要求,对于需要二次包封的产品基岛建议采用分割设计,在同等条件下,类似四宫格、六宫格、九宫格等分割设计能有效地减少焊锡空洞过大风险,分别如图3-80和图3-81所示。

图3-79 芯片布局建议与不建议设计示例图

图3-80 单个基岛的焊锡空洞示意图

图3-81 分割基岛后的焊锡空洞示意图
7. 塑封料包封不良与空洞
一些大芯片或大元器件底部与顶部极易出现填充不良问题,对于顶部可能出现的包封不良风险,主要考虑所封芯片或元器件的尺寸、材料、模具、切割道与切割刀的选择设计是否适当,在单个芯片内部设计规则时要选择边距控制模式,如图3-82所示。在图3-82中,B需要根据芯片尺寸及材料而定,一般根据芯片尺寸而定,若X为某一最小边距值,则
芯片尺寸≤6mm2,B≥X
6mm2<芯片尺寸<36mm2,B≥2X
芯片尺寸≥36mm2,B≥3X
元器件与封装边距都有一定的距离设计要求,否则加工完成后会产生包封不良问题。

图3-82 塑封料边距控制模式
除前面介绍的布局合理性、元器件与芯片之间的密集度会造成填充空洞外,底部通常也需要优化元器件所对应的绿漆开口设计,从而使塑封料可以充分填充元器件底部间隙。塑封料元器件底部充分填充如图3-83所示。

图3-83 塑封料元器件底部充分填充
元器件底部对应的基岛之间增加绿漆开口设计。开口超出元器件尺寸的设计不仅有利于增加元器件与基板的距离,也有利于塑封料的流动与填充,降低塑封料空洞的风险。对于BGA、LGA之类的元器件,让四周绿漆开口尺寸适当大于元器件尺寸,也可以增加元器件与基板的距离,利于塑封料的填充,降低包封空洞的风险。
可靠性失效还有很多模式,上述常见可靠性设计只列举了很少的一部分,行业内一般都有较为详细的设计规则,这些规则既是可制造性经验的总结,又整合了常用可靠性设计规则。设计师在设计封装时,需要参阅各厂家的封装设计规则,熟练应用,以尽可能在设计阶段规避不必要的风险。由于可靠性设计涉及结构、材料、集成工艺、使用环境、电性分析、散热、应力等多种因素,因此在前期设计阶段需要综合评估。