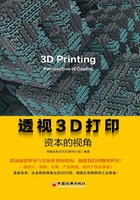
4.5 其他3D打印技术
4.5.1 分层实体制造(LOM)
LOM工艺称为分层实体制造,是历史最悠久的3D打印成型技术,也是最成熟的3D打印技术之一,由美国Helisys公司的Michael Feygin于1986年研制成功。
4.5.1.1 LOM工作原理
LOM系统主要包括计算机、数控系统、原材料存储与运送部件、热黏压部件、激光切系统、可升降工作台等部分组成。LOM以片材为原材料,如纸、塑料薄膜等。片材表面事先涂覆上一层热熔胶。加工时,热压辊热压片材与下面已成形的工件黏接;用CO2激光器在刚黏接的新层上切割出零件截面轮廓和工件外框,并在截面轮廓与外框之间多余的区域内切割出上下对齐的网格;激光切割完成后,工作台带动已成形的工件下降,与带状片材分离;供料机构转动收料轴和供料轴,带动料带移动,使新层移到加工区域;工作台上升到加工平面;热压辊热压,工件的层数增加一层,高度增加一个料厚;再在新层上切割截面轮廓。如此反复直至零件的所有截面黏接、切割完,得到分层制造的实体零件。

图4-47 LOM工作原理图
资料来源:华融证券。
4.5.1.2 LOM优缺点
1.LOM优点
(1)原型精度高,在薄片材料的切割成型中,纸材一直都是固态,仅有一层薄薄的胶从固态变化为熔融态。所以,LOM制件没有内应力,而且翘曲变形小。在x方向的精度是0.1毫米~0.2毫米,y方向和x方向精度相同,在z方向的精度是0.2毫米~0.3毫米。
(2)原型能承受高达200℃的温度,有较高的硬度和较好的力学性能。
(3)无须额外设计和制作支撑。
(4)废料、余料易剥离,可进行各种切削加工,无须后固化处理。
(5)成型速度快,该技术不需要对整个断面进行扫描,而是沿着工件的轮廓由激光束进行切割,具有较快的成型速度,因此可以用于结构复杂度较低的大型零件的加工,制作成本低。
2.LOM缺点
(1)有激光损耗,并且需要建造专门的实验室,维护费用昂贵。
(2)可以应用的原材料种类较少,目前最常用的是纸材,不能直接制作塑料工件。
(3)纸材的最显著缺点是对湿度极其敏感,LOM原型吸湿后叠层方向尺寸增长,严重时叠层会相互之间脱离。为避免因吸湿而引起的这些后果,在原型剥离后短期内需要迅速进行密封处理。
(4)工件的抗拉强度和弹性不够好,且工件表面有台阶纹,很难构建形状精细、多曲面的零件,仅限于结构简单的零件。成型后需进行表面打磨。
(5)制作时,加工室温度过高,容易引发火灾,需要专门的人看守。
4.5.1.3 LOM厂商及应用
美国Helisys公司1990年前后开发了第一台商业机型LOM-1015,其后推出LOM-1050和LOM-2030两种型号成型机。
研究LOM工艺的公司除了Helisys公司,还有日本Kira公司、瑞典Sparx公司、新加坡Kinergy精技私人有限公司、清华大学、华中理工大学等。

图4-48 LOM-1015
LOM是几种最成熟的快速成型制造技术之一。这种制造方法和设备自1991年问世以来,得到迅速发展。由于叠层实体制造技术多使用纸材,成本低廉,制件精度高,而且制造出来的木质原型具有外在的美感和一些特殊的品质,因此受到了较为广泛的关注。
应用领域:工业设计、机械制造、汽车零部件制造、模具、艺术品设计、动漫行业、军工保密单位以及航空航天、高等教育、建筑装饰、外科医疗(骨科应用较多)、儿童玩具制造、制鞋行业等。在产品概念设计可视化、造型设计评估、装配检验、熔模铸造型芯、砂型铸造木模、快速制模母模以及直接制模等方面得到了迅速应用。
图4-49是某车灯配件公司为国内某大型汽车制造厂开发的某型号轿车车灯LOM原型。

图4-49 LOM应用实例
4.5.1.4 LOM原材料
LOM材料一般由薄片材料和热熔胶两部分组成。
(1)薄片材料。根据对原型件性能要求的不同,薄片材料可分为:纸片材、金属片材、陶瓷片材、塑料薄膜和复合材料片材。
当前纸片材应用最多。这种纸由纸质基底和涂覆的黏结剂、改性添加剂组成,成本较低。
(2)热熔胶。用于LOM纸基的热熔胶按基体树脂划分,主要有乙烯-醋酸乙烯酯共聚物型热熔胶、聚酯类热熔胶、尼龙类热熔胶或其混合物。
目前,EVA型热熔胶应用最广。EVA型热熔胶由共聚物EVA树脂、增黏剂、蜡类和抗氧剂等组成。
4.5.2 激光近形制造技术(LENS)
20世纪90年代中期,UTC与美国桑地亚国家实验室(Sandia National Laboratories)合作开发了使用Nd:YAG固体激光器和同步粉末输送系统的全新理念的激光近形制造技术(Laser Engineered Net Shaping,LENS),成功地把同步送粉激光熔覆技术和选择性激光烧结技术融合成先进的激光直接快速成型技术。
4.5.2.1 LENS原理
LENS技术将快速成型技术中的选择性激光烧结技术和激光熔覆成型技术结合,其基本原理如图4-50所示。该系统主要由4部分组成:计算机、高功率激光器、多坐标数控工作台和送粉装置。在计算机上生成零件的CAD模型,然后使CAD模型离散为一系列二维平面图形,计算机由此获得扫描轨迹指令。激光束通过光学系统被导入加工位置,与金属基体发生交互作用形成熔池,金属粉末通过送粉器经送粉喷嘴在保护气体的作用下汇集并输送到激光形成的微小熔池中,熔池中粉末熔化、凝固后形成一个直径较小的金属点。根据CAD给出的路线,数控系统控制激光束来回扫描,便可通过点、线、面的搭接以及逐层熔覆堆积出任意形状的金属三维实体零件。

图4-50 激光近形制造技术的基本原理示意
4.5.2.2 LENS优缺点
激光束具有高功率密度、方向性好、控制快捷等优点,从而使激光近形制造技术具有快速、准确、经济等优点,特别是该技术对零件的复杂程度没有限制。同时,金属材料在激光束的照射下所获得的优越组织性能还可保证零件具有优越的性能。具体如下:
1.优点
(1)LENS技术在加工异质材料方面的特有优势是,采用LENS技术可以很容易地实现零件不同部位具有不同的成分和性能,不需反复成形和中间热处理等步骤。
(2)激光直接制造属于快速凝固过程,金属零件完全致密、组织细小,性能超过铸件。
(3)不需采用模具,使制造成本降低15%~30%,生产周期节省45%~70%。
(4)如果系统的整体性较好,参数合理,LENS技术制成的模型或者零件的微观组织中无夹杂、无气孔、无凹陷、无裂纹,致密度达100%。对采用LENS技术制成的试样进行疲劳测试,结果显示,其制成成形件的疲劳强度高于相应铸件以及锻件的疲劳强度。
2.缺点
(1)制件成形效率较低,其堆积速率较慢。
(2)采用LENS技术建成的成形件表面质量较为粗糙,一般不能直接使用,需要后加工来提高表面质量。
(3)整个过程需要惰性气体保护,而且使用的是金属粉末,成本较高。
4.5.2.3 LENS厂商及应用
目前LENS技术较多地用于高价值金属航空航天零件的制造、修复及改型。
1998年以来,Optomec公司致力LENS技术的商业开发,推出第三代成形机LENS850-R设备。2013年,Optomec公司推出新的金属3D打印机产品LENS 450。LENS 450的核心技术与LENS系列的其他产品类似,都是用来修复、电镀和快速生产多种高性能金属部件。LENS沉积系统使用高功率激光的能量,在瞬间直接将金属粉末变成结构层。
在国内,西北工业大学研究的激光立体成型和北京航空航天大学采用此方法成型大型钛合金件,在航空航天等重要工业领域的应用迅速发展。
4.5.2.4 LENS原材料
LENS技术适于钛合金等高强度金属件加工。LENS技术选用的金属粉末有三种形式:
(1)单一金属。
(2)金属加低熔点金属黏结剂。
(3)金属加有机黏结剂。由于采用的是展粉方式,所以不管使用哪种形式的粉末,激光烧结后的金属的密度较低、多孔隙、强度较低。要进一步烧结零件强度,必须进行后处理,如浸渗树脂、低熔点金属,或进行热等静压处理。但这些后处理会改变金属零件的精度。