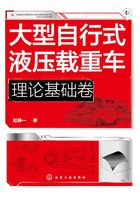
第一节 液压载重车的液压驱动系统设计要求
一、闭式液压系统介绍
液压载重车动力舱置于车辆的中端,驱动组件置于车辆的两端,距离很远,整车形态复杂,结构紧凑,尺寸跨度很大。模块车在行驶过程中外负载惯性大,且正反向换向及制动比较频繁,是适合于负荷变化剧烈和前进、倒退、制动频繁的工程机械负荷工况,以及对速度要求严格控制的作业机械。
1.闭式系统构成
自行式液压载重车最理想的传动方式是采用闭式泵⁃马达减速器的闭式回路。按布局形态可分为“整体式”和“分置式”两类;按液压马达与行走装置之间的连接,有“高速方案”和“低、中速方案”;按泵、马达数量可分为单泵单马达、单泵多马达、多泵多马达等。
采用双向变量液压泵,通过泵的变量改变主油路中的流量大小和方向,实现车辆的变速与换向。闭式系统的主泵上通轴附设一小排量齿轮(或内齿轮)补油泵,补油溢流阀和补油单向阀多集成于主泵,冲洗冷却阀集成在马达上。补油溢流阀调定补油压力,补油单向阀选择补油方向,向主油路低压侧补油,以补偿由于泵、马达容积损失及由冲洗冷却阀泄漏掉的流量。由于系统是闭式回路,马达出口的油液大部分又进入闭式泵的进油口,而不是回油箱,所以油温通常很高,必须在系统回路上安装冲洗阀,使马达低压侧的一部分热油通过冲洗阀,经冷却后流回油箱,油箱的冷却油通过补油泵重新进入系统中。冲洗阀可以集成在马达上,也可以单独安装在系统中。由于油液发热的原因,需要有部分冷却油不断地流入系统,补充冲洗掉的热油,补油泵的存在使系统增加了一部分很小的稳定的附加损失。但其排量和压力相对于主泵均很小,因此其附加功率损失通常仅为传动装置总功率的1%~2%,可以忽略不计(其原理如图4⁃1所示)。

图4⁃1 闭式液压系统原理图
2.闭式系统优点
① 闭式系统结构紧凑,变量泵均为集成式构造,减小了安装空间。系统管路连接相对简单,减少了管路布置的工作量,简化了操作。闭式系统由于采用了双向变量泵和变量马达,换向、制动方便,适用于换向、制动频繁的驱动系统。改变泵和马达的排量就可以改变马达的转速,不会产生节流损失,系统效率高。
② 补油泵通常还用于对主泵和马达进行冷却,让多余的流量通过主泵和马达壳体回油箱,这种冷却对防止主泵、马达长时间在零流量或零压力(或持续高压大功率)下工作产生的过热是必要的。因为在零压力下主泵、马达一般无内泄漏,持续大功率下则热量过多。补油泵还能方便地为某些低压工作的辅助机构和制动器提供动力,这种情况下安装一个顺序阀即可保证主回路不受辅助回路影响,防止因补油不足而停车;仅有少量的补油流量从油箱吸取,油箱小,便于行走车辆布置。
③ 闭式系统通过补油泵的补油,能够有效防止变量泵在大流量时因为吸空导致的气蚀现象,提高泵的工作转速和传动装置的功率密度。此外,在补油泵出口安装一个较小流量的压力滤油器,使工作介质经过滤后进入系统,提高传动装置的可靠性和寿命。确保主泵的进油口压力恒定在调定压力,从而使泵工作时不易损坏,可靠性更高,使用寿命更长。
④ 闭式系统工作时由于补油溢流阀的原因背压较为恒定,A油口和B油口对称工作。柱塞泵和马达的容积效率不低于85%,并且工作时泄漏量基本不随压力变化。这些特点使得闭式系统在工作时柱塞泵从正转向反转过渡平稳,不会出现流量脉动,输出轴刚性较大,负荷有变化时仍能平稳地工作。
二、液压载重车的液压驱动系统设计
闭式液压系统是液压传动的一种形式,适用于外负载惯性大且换向频繁的机构,特别是结构要求紧凑的大型工程机械的驱动系统。闭式液压系统是由液压泵和液压马达组成的容积调速系统,通过调节液压泵或液压马达的排量来调节马达的转速或转矩。如果采用变量液压泵和变量液压马达传动,则系统完全可以实现无级调速。闭式液压系统具有功率密度高、布局方便、过载保护能力强和控制方式灵活等特点。
载重车的液压驱动系统采用变量泵⁃变量马达容积调速回路,通过对系统转速特性和转矩特性的分析,可以为液压驱动系统的设计提供理论依据。
载重车行驶时的受力方程为
Ft=Ff+Fp+Fm(4⁃1)
式中 Ft——载重车驱动力,N;
Ff——载重车行驶摩擦阻力,N;
Fp——载重车坡道阻力,N;
Fm——载重车加速阻力,N。
马达的转矩特性可以表示为
Mm==
(4⁃2)
式中 Mm——马达输出转矩,N·m;
rd——轮胎承载半径,m;
n——驱动轮胎数量;
id——减速器传动比;
Δpm——马达进出口压差,bar(1bar=100kPa,下同);
qm——马达的排量,m3/r;
ηmm——减速器机械效率。
马达的转速特性可以表示为
nm=ηvm=
=
(4⁃3)
式中 nm——马达转速,r/mim;
Qam——马达流量,m3/min;
ηvm——马达的容积效率;
Qap——泵的流量,m3/min;
qp——泵的排量,m3/r;
np——发动机的转速,r/min;
ηvp——泵的容积效率。
以JHP270ZXP为例,根据整车驱动力及速度的要求,经过计算,确定选用A4VG 125/32变量柱塞泵2台,A6VM 55/63马达8台。根据已知发动机及轮胎的参数,得到液压驱动系统的驱动力⁃速度曲线,如图4⁃2所示。图4⁃2关键点的数据在表4⁃1中列出。

图4⁃2 载重车驱动力⁃速度曲线
1daN=10N
表4⁃1 液压系统关键点数据

图4⁃3为JHP270ZXP载重车的液压驱动系统原理图。
三、液压载重车的驱动布置方案选择
为了实现大型自行式液压载重车设计意图与目标,关键在于做好驱动总体方案设计。为了做好整体方案设计,首先结构形式要处理好,主要参数要确定好,在出现矛盾时,要先保证主要工况,再照顾好次要工况。由于载重车载重吨位大、自重较大且额定行驶速度不能定得太高,应力求高度低、结构简单,以提高整机横向稳定性。
首先根据用户提出的使用路况的特点及转向工况等使用条件,确定载重车应当采用轮胎式结构方案,而否定了履带式结构的方案。图4⁃4所示为轮式工程运输机械行走机构液压传动的四种基本型式,图中元件的数量仅为示意,并非实际数目。


图4⁃4 液压传动布置方案
1—液压泵;2—液压马达;3—变速箱;4—万向节;5—差速器;6—轮胎;7—发动机;8—轮边减速器
图4⁃4(a)为液压传动代替离合器等机械传动的结构,保留了传统的齿轮变速箱3、传动轴、万向节4及轮间差速器5。这种传动方式系统简单、制造成本低,但不能改善轮式机械行走机构的性能和牵引动力特性。
图4⁃4(b)给出了一种具有闭合回路的全液压系统。换向靠大扭矩液压马达反转。马达2直接装在车轮上,无需轮边减速装置。这种系统的缺点是在一定功率时的调速范围很小(不超过5km/h),外廓尺寸大,不能获得超过15km/h的速度,其单位重量和单位功率传递值均比带减速装置的高速马达小。国外采用这种传动方式的较多,一般用于低速运行机械。
图4⁃4(c)所示为高速小扭矩液压马达经过减速装置8驱动车轮的传动系统。它可以利用已经成熟的车轮马达系列,并保证马达有较高的工作效率。在这样的系统中,可以用定量马达,也可以用变量马达。采用变量马达时,由于柴油机转速和排量也可调,机器行走速度调节范围可达25km/h,最大行走速度50km/h。采用这种传动方案,除可改进液压系统传动参数外,还能采用标准化的车轮液压马达系列。
图4⁃4(d)全部采用变量泵和变量马达驱动,消除了上述许多弊病。同时,由于柴油机转速可调,因而大大提高了轮式工程机械的牵引动力特性。这样的系统适用于大多数轮式载重车。采用变量泵⁃变量马达,调速范围扩大了,并可以考虑布置不同的驱动与从动桥,前面的驱动桥和后面的驱动桥能分配不同的负荷比率。这种方案具有较高的牵引动力特性。
经过比较上面四种传动布置方案的优缺点并反复设计计算以后,选定载重车行走驱动系统传动布置方案为图4⁃4(d)所示的方案,图4⁃5所示为驱动系统的布置图。

图4⁃5 驱动系统布置图
四、整车调速控制
为确保车辆在正常作业的情况下,提高车辆效率、行驶的操控性和平稳性,必须根据车辆的不同行驶工况来调节载重车行驶速度。载重车采用液压传动,由发动机直接带动变量泵,变量泵驱动变量马达,通过轮边减速器直接驱动轮胎,中间没有变速箱,不能像一般车辆那样通过选择不同挡位来调节车速。另外由于系统需要,发动机的输出转速需保持恒定,又不能通过调节发动机的输出转速来调节车速。因此,载重车的速度调节利用液压传动的特点,通过调节变量泵和变量马达的排量来调节速度,和一般车辆相差很大。启动前将马达的排量调到最大值,将泵的排量调到零位。启动后,首先调节泵的排量,逐渐调到最大值;然后再将马达的排量从最大值往小调。调节泵的过程中,马达的排量不变,此时相当于变量泵⁃定量马达的回路特性,为恒扭矩工况。而调节马达的过程中,泵的排量保持不变,又相当于定量泵⁃变量马达的回路特性,为恒功率工况。将这两种回路的调节结合起来,就是变量泵⁃变量马达回路的调节方式。

图4⁃6 变量泵⁃变量马达组成的容积调速回路的输出特性曲线
自行式全液压载重车变量泵⁃变量马达容积调速回路特性曲线如图4⁃6所示。图中,曲线abc表示车辆驱动力矩,曲线def表示车辆行驶速度。
1.启动加速阶段(恒扭矩调速阶段)
相当于变量泵⁃定量马达容积调速。运输车从静止状态到运动状态,其负载基本不变,马达输出扭矩为Mm=1/2πqmΔp。当负载不变时,Δp不变,而定量马达的流量值是不变的,所以马达的输出扭矩为恒值(如图4⁃6线段ab),
与马达转速的变化无直接关系。马达输出功率为Nm=2πnmMm,Mm恒定,所以马达输出功率与马达转速呈线性关系。由于运输车起步阶段负载大,故马达的输出扭矩必须足够大才能驱动车起步,此时马达的排量保持最大,泵的输出转速不变。而马达的转速nm(nm=npqp)/qm与泵的排量qp成正比。随着变量泵斜盘倾角增大,泵的排量随之增大,使马达转速上升,马达的输出功率增大(如图4⁃6线段de)。随着变量泵从最小排量调到最大排量,马达转速相应从最小转速nm min逐渐提高到与泵最大排量相应的转速n为止。
2.行驶阶段(恒功率调速阶段)
相当于定量泵⁃变量马达容积调速。此阶段泵的排量最大,并保持不变。马达的输出功率为Nm=2πnmMm=Qp·Δp。当外负载不变时,Δp不变。所以马达的输出功率保持恒定,如图4⁃6中线段ef,由该公式又可知,在变负荷工况下,马达的输出转矩Mm与转速nm成反比例关系,基本按图4⁃6线段be所示的双曲线关系自动调节。随着负载的减小,马达从最大排量自动减小到某一限定值,转速相应继续提高到马达所能达到的最大转速。此阶段马达转速随负载变化自动调节,保持马达输出功率恒定。
调节载重车的行驶速度,主要通过调节变量泵和变量马达的排量来实现,调节变量泵的排量实际上是改变变量泵的输出流量。在任何情况下,需保证有足够的驱动力来驱动车辆。欲改变车辆的驱动力,可通过调节变量马达的排量和变量马达的有效工作压力来实现。根据车轮驱动系统液压原理,在马达排量确定的情况下,马达并联油路的压力通常情况下取决于载重车在行驶作业过程中的车轮阻力,而这与车辆的承载有关。载重车重载时,阻力较大,系统压力也较高。反之,载重车轻载时,车轮阻力小,则系统压力低。因此,整个系统的压力是被动的,随着不同工况时工作阻力不同而改变。从控制本身的角度来考虑,有一定的自适应性,这也是静液压传动方式的一个优点。有时为了适应特殊工况,有必要维持系统工作压力恒定,这就是通常所说的恒压控制问题。
五、差速控制
车辆在行驶过程中,特别是转弯时,每个车轮的转速是不一样的,尤其是在多轮驱动的情况下,如果不加以调节,就会出现个别车轮打滑现象。为了保证车辆行驶的稳定性和操纵性能,使车辆在行驶过程中,能够根据行驶状况的要求,自动调节各驱动轮的行驶速度,使驱动轮在行驶过程中始终和地面保持纯滚动,这就是自动差速控制。传统的汽车差速是通过一个机械差速器来实现的。载重车驱动桥上是由变量马达直接驱动车轮的,中间没有差速器。
以JHP270平板车为例,有5条轴线,应有约1/3为驱动轴,其余为从动轴,共有8个变量马达,这8个变量马达并联在系统的公共回路上。当载重车行驶时,在不作任何调节的情况下,变量马达的工作压力取决于负荷最低的那个驱动轮的工作阻力。因所有马达都并联在公共回路上,每个马达的进口压力都应当相同,也就是整个系统的压力取决于行驶过程中负荷最小的那个驱动轮的阻力。当所有轮胎与地面保持良好的接触即纯滚动时,只要所有马达所产生的总牵引力足够克服负荷产生的总阻力,静液压传动系统本身就能较好地实现差速性能。
当车辆转弯时,每个车轮的转速都不一样,外圈的车轮转速大于内圈车轮的转速。如果这时内外圈车轮转速一样,则外圈车轮必定发生滑移。由于所有车轮和地面保持纯滚动,并且马达所产生的总牵引力能够克服负载所产生的阻力驱动车辆前进,如果车轮想要发生滑移,则必然会产生一个阻止车轮滑移的阻力,这个阻力在一定程度上起到提高车轮转速的作用。静液压传动最大的特点是不同于其他传动方式的硬特性,其他传动方式一旦给定了输出转速,除了人为调节之外,是不会随着外界条件而变化的。静液压传动的性能较柔,具有自适应性。因此,当车轮受到一个强制加速的力时,系统会自动调节分配给驱动这个车轮的马达相应的流量,这就是静液压传动系统的自动分流的特性。利用这个特点可以较好地解决运输车的差速问题。这也是一般驱动轮较多的车辆都采用液压传动的一个原因。
六、防滑控制
闭式驱动系统有一个缺点:当某个马达所驱动的车轮的附着力不够时,该车轮会出现打滑现象,轻微时,机器卸载后可驶出打滑区域;严重时,车辆无法脱离泥沼或坑陷而发生“陷车”。目前,国内采用闭式液压驱动系统的机械一般都没有采取措施进行防滑控制,而是等车辆出现打滑后将车停下来另想办法使其驶出打滑区域。
1.车轮打滑的产生原因及其危害
根据行驶原理,车辆行驶必须同时满足驱动条件和附着条件,即为:
Ff+Fw+Fi≤Ft≤FZφφ(4⁃4)
式中 Ft——汽车的驱动力;
Ff——滚动阻力;
Fw——空气阻力;
Fi——坡道阻力;
FZφ——驱动轮上支撑的重力;
φ——附着系数。
当车辆提供的驱动力足够大而附着力不足时,驱动力的最大允许值由附着力决定。若此时行驶总阻力超过附着力,则车辆由于驱动轮产生严重滑转而不能正常工作。
车辆行进过程中,车速和车轮转动线速度(轮速)之间存在着速度差,也就是车轮与地面之间有滑移现象。一般用滑转率S来表示滑移的程度。
S=(ωR-v)/ωR×100%(4⁃5)
式中 ω——车轮的角速度,r/s;
R——车轮的动力半径,m;
v——汽车的速度,m/s。
当车速v=0时,S=100%,即车轮在原地打滑;当v=ωR时,S=0,表明车轮做纯滚动;当0<S<100%时,车轮既滚又滑。
典型的车轮传动装置采用几个车轮马达并联的方式,由液压泵为其提供动力。当车辆行驶时,在不作任何调节的情况下,变量马达的工作压力取决于负荷最低的那个驱动轮的工作阻力。车辆行驶过程中的牵引力是一个被动力,由驱动车轮的马达的输出转矩决定,它随着马达输出转矩的增大而增加,随着马达输出转矩的减小而降低,但又受到地面等条件的制约,其增加不是无限制地增加,而必须不超过地面对车轮的最大静摩擦力,否则会出现车轮打滑。而地面给车轮的最大静摩擦力取决于地面的附着系数,影响附着系数的因素很多,如路面条件、附着重量、轮胎充气压力、轮胎尺寸、轮胎花纹、轮胎结构等。一旦某个车轮出现打滑,系统中其他车轮的压力和扭矩就会被限制在同一水平。在极端状况下,一个车轮悬空会使其他车轮的压力降为零。在这种情况下,不但主机的牵引力会丧失,而且空转的马达也会由于超高速运转而损坏。因此,必须采取措施进行行走机械闭式液压驱动系统防滑控制。
2.车轮打滑的检测
各变量马达上都装有转速传感器,利用各驱动轮的转速值,可检测车轮是否处于打滑状态。其原理方法如下:
① 每个驱动轮的车轮马达内都装有传感器,传感器安装在变量马达专门的测量孔中,对应一个由磁性材料制造的内置齿轮或类似部件,传感器用霍尔效应半导体检测磁通量的变化。当车辆行驶时,变量马达转动带动齿轮转动,传感器发出相应的脉冲信号,并把检测到的磁通量变化转换为脉冲方波信号,通过控制器在单位时间内对脉冲信号计数,计算出相应驱动轮的转速。
② 在平坦的路面直线行驶时,各个车轮的转速在理论上是相等的。取所有驱动轮的转速的平均值为基准,并设定一个误差范围Δn,若某一个驱动轮的转速超出
+Δn这个范围时,则认为这个车轮开始打滑,需要进行调节,这也是自动控制的一个条件。
③ 当车辆转弯时,根据控制装置输入的转角计算出每个轮胎的转向角,则每个驱动轮在转向时的转速ni可以通过式(4⁃6)确定。同样设定一个转速范围ni+Δn,当驱动轮转速超出这个范围时,则确认此驱动轮打滑。
ni=f(R,v,z)(4⁃6)
式中 R——相应车轮的转弯半径;
z——转向中心所处的车轴距车第一轴的距离。
3.车轮打滑液压控制方法
行走机械闭式液压驱动系统防滑常用的控制方法有三种:一是调整打滑驱动轮马达上的转矩,二是限制打滑驱动轮马达的流量,三是对发生打滑的驱动轮直接施加制动控制。
(1)调整马达输出转矩防滑
首先分析行走机械发动机⁃液压泵⁃液压马达转矩匹配原理。发动机的输出功率为:
Pe=(4⁃7)
式中 Pe——发动机的输出功率,kW;
Me——发动机的输出转矩,N·m;
ne——发动机的输出转速,r/min。
液压泵的输出功率为:
Pp=(4⁃8)
式中 Pp——液压泵总的输出功率,kW;
Δpq——驱动液压泵的压差,MPa;
Vq——驱动液压泵的排量,mL/r;
nq——驱动液压泵的转速,r/min。
马达的输出功率可以表示为:
Mm==
(4⁃9)
(4⁃10)
式中 Mm——马达输出转矩,N·m;
Δpm——马达进出口压差,bar;
qm——马达的排量,mL/r;
nmi——马达的转速,r/min。
在不考虑功率过载余量和传动效率的情况下,发动机功率、泵输出功率和马达输出功率三者相等,即:
(4⁃11)
泵和马达之间还存在着流量匹配的关系,即:
(4⁃12)
从上式可以看出,调整马达输出扭矩的方法有很多,可以通过改变液压泵或马达的排量来实现,也可通过调整发动机的输出转矩来实现。分如下情况讨论:
① 对于变量泵⁃变量马达系统和定量泵⁃变量马达系统,一般考虑调整打滑马达的排量。当某组驱动轮发生滑转时,将滑转的马达排量按照一定的算法减小,使得马达输出扭矩减小,直至打滑侧转速下降,系统压力重新建立,流量大部分分配到未滑转一侧,该侧地面附着条件较好时,能提供主要的牵引力,而滑转的一侧也可通过控制算法提供一定的辅助牵引力,使车辆脱离打滑区域。在减小滑转侧马达排量过程中,是否会出现因马达排量减小,反而转速升高,滑转更为严重,甚至排量接近零时的马达“飞车”现象是一个值得考虑的问题。解决这种问题的思路有多种,如下:
a.给悬空车轮予以制动;
b.设置旁路阀,使该液压马达旁路,同时切断与液压泵的油路;
c.当马达排量连续减小到一定值时,若马达车轮仍打滑,则将其排量以阶跃信号的形式快速调节至零。
从控制系统本身的角度出发,这里提及的几种方法都可行。但考虑到在工程应用中,应力求控制方式简单,易于实现,因此考虑选用第三种方案。
② 对于变量泵⁃定量马达系统,由于马达排量不能改变,只能通过改变液压泵排量或调整发动机的输出扭矩来调节马达的输出扭矩。柴油机常通过控制燃油喷射量来减低其输出转矩。同时,还可以加大泵的排量来降低液压系统的压力,这样也能减小打滑车轮马达的输出扭矩。当调整到式(4⁃12)满足时,车辆就可以重新建立平衡,驶出打滑区。
③ 对于定量泵⁃定量马达系统,只能通过调整发动机的输出扭矩来调节马达的输出扭矩。这种系统调整的范围比较小,一般通过别的方式来解决打滑问题。
(2)限制打滑驱动轮马达的流量防滑
因为所有马达都是并联在公共回路上,当某个车轮打滑时,系统压力下降引起泵的输出流量全都进入打滑马达导致车辆不能正常工作。如果能控制进入打滑马达的流量,就能控制马达的转速,解决马达打滑的问题。这种方法不论泵、马达排量能否调整均适用。限制打滑驱动轮马达的流量有三种方法:
① 采用分流集流阀 分流集流阀也可以进行牵引控制,分流集流阀依据负载传感原理分配各支路的流量。液压油通过分流集流阀阀芯窗口流向马达时产生压力降。由于通过阀孔的流量不同,因而作用于尾部腔内所产生的压力也不同,从而使阀芯移动,并限制过高的流量通过。流量分流集流阀的设计不会由于精确度过高而导致由于转向和地面不平所引起的车轮正常打滑。流量传感分流集流阀在液压油流向相反的情况下便如此工作。其缺点在于分流集流阀的有限工作流量范围较窄,在用于速度变化范围较大的设备时,由于工作时低速动转,移动时高速,那么当液压油在闭式回路中通过阀孔时,压力下降十分明显,这样就会使驱动车轮的动力下降并产生热量。
② 采用流量控制阀 采用流量控制阀控制系统打滑的原理如图4⁃7所示,每个马达上均装有速度传感器和可调节流阀。当传感器检测到某个马达超速时,控制器发指令给相应的可调节流阀,减小流向该马达的流量,这样就可以有效防止马达打滑,且系统压力仍能维持在一个相对较高的水平,整车仍能正常行驶。

图4⁃7 流量控制阀控制打滑原理图
③ 将打滑马达与泵断开 可以通过两种途径实现,一种是采用旁通阀,另一种是迅速将马达排量调整为零。解决压力下降的方法是使用靠电磁驱动的旁通阀。这种类型的旁通阀在进行高速运输以及没有牵引问题的情况下,可以使液压油不经过分流阀流向马达,从而使液压油压力不受限制。旁通阀的这种性质可以在不影响系统的正常工作状态下改变车轮马达的排量。只有当设备在一定的速度范围内,所有的马达都达到同样的排量时,分流阀/阀组才能启动。也可以用一个换向阀将马达的进出口连通,并与主油路切断,将打滑马达变成一个从动轮。或者将马达排量直接调整到零变成从动轮。
(3)对发生打滑的驱动轮直接施加制动控制打滑
马达打滑的原因就是该马达的驱动力大于附着力,要想通过对发生打滑的驱动轮直接施加制动控制打滑,就要求系统中每一个驱动轮均装有独立的制动器。当传感器检测到某个马达打滑时,控制器发出相应指令,对该马达实施制动控制,直至满足其驱动力小于附着力为止。也可考虑将打滑的车轮马达排量减小。减少驱动该车轮的马达排量,其所能产生的输出转矩相应减小。这样就不会因为某个车轮的行驶阻力较小,而导致整个系统的工作压力下降。其他正常行驶的车轮的马达仍然维持原先的排量,即维持正常行驶时的输出转矩。当打滑的驱动轮恢复至纯滚动时,则驱动该车轮的马达的排量又自动恢复到最大值。