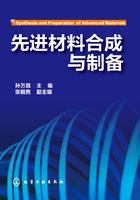
2.3 化学气相沉积技术
化学气相沉积(chenmical vapor deposition, CVD)是一种化学气相反应生成法,在不同的温度场、不同的真空度下, 将几种含有构成涂层材料元素的化合物或单质反应源气体, 通入放有被处理工件的反应室中, 在工件和气相界面进行分解、解吸、化合等反应,生成新的固态物质沉积在工件表面,形成金属或化合物的薄膜层。通过控制反应温度、反应源气体组成、浓度、压力等参数,就能方便地控制涂层的组成结构和成分,改变其力学性能和化学性能,满足不同条件下对工件使用性能的需求。
利用这种方法可以制备的薄膜种类很广泛,如金属和介质薄膜、耐磨涂层、高温保护涂层等。CVD法制备薄膜的沉积速率快、膜层的均匀性好、具有优异的台阶覆盖性能,适宜在复杂的基片上镀膜。
从沉积化学反应能量激活看,化学气相沉积技术可分为热CVD技术、等离子辅助化学气相沉积技术(PACVD)、激光辅助化学气相沉积技术(LCVD)和金属有机化合物沉积技术(MOCVD)等。从沉积化学反应温度来看,又可分为低温沉积、中温沉积、高温沉积。从沉积反应的类型看,可分为固相扩散型、热分解型、氢还原型、反应蒸镀型和置换反应型。
2.3.1 化学气相沉积理论
2.3.1.1 CVD反应方程式
由于制取涂层材料的不同,在CVD技术中会采用不同的化学反应类型。如热分解反应、金属还原反应、化学输送反应、氧化或加水分解反应、等离子激发反应、光激发反应等。在实际应用中,最常见的CVD反应方式有以下几种。
(1)氧化还原反应
在沉积反应中,至少有一个元素被氧化或还原,如果在反应中涉及氢,通常叫氢还原反应。属于这类的CVD反应很多,例如:
(2-21)
(2-22)
(2-23)
(2-24)
(2)歧化反应
若元素在气相中存在两种氧化状态,利用变价特点,可以提纯或沉积某些物质, 如:
(2-25)
(2-26)
(3)合成或置换反应
在反应中发生了置换或合成。属于这类反应的也很多,如:
(2-27)
(2-28)
(4)金属有机化合物反应
为了降低CVD沉积温度,可以选用金属有机化合物进行热分解,称为MOCVD,如:
(2-29)
(2-30)
(5)形成化合物
由两种或两种以上的气态物质在加热的衬底表面上发生化学反应而沉积出固态薄膜,这种方法是化学气相沉积中使用最普遍的方法,如:
(2-31)
(2-32)
(6)激发反应
利用等离子体、紫外线、激光等方法,使反应气体在基片上沉积出固态薄膜的方法。如:
(2-33)
(7)化学输送反应
在高温区被置换的物质构成卤化物或者与卤素反应生成低价卤化物,它们被输送到低温区域,由非平衡反应在基材上形成薄膜,如:
(2-34)
(2-35)
(2-36)
在CVD 过程中,只有发生在气-固交界面的化学反应才能在基片上形成致密的固态薄膜;如果发生在气相,生成的固态薄膜只能以粉末状存在。由于CVD中气态反应物的化学反应和反应产物在基片的析出过程中是同时进行的,因此,CVD的机理比较复杂。CVD中化学反应受气相与固相表面接触催化作用的影响,并且其产物的析出过程也是由气相到固相的结晶生长过程。
2.3.1.2 CVD反应过程
CVD反应是在基体表面或气相中产生的组合反应,是一种不均匀系反应。它涉及化学反应、热反应、气体输送及涂层生长等方面的问题。根据反应气体分析、排出气体分析和光谱分析,其反应过程一般认为有以下几步。
①反应气体(原料气体)到达基体表面。
②反应气体分子被基体表面吸附。
③在基体表面上发生化学反应,形成晶核。
④固体生成物在基体表面解吸和扩散,气态生成物从基体表面脱离移开。
⑤连续供给反应气体,涂层材料不断生成。
在这些过程中,反应最慢的一步决定了整个反应的沉积速率。
2.3.1.3 CVD反应条件
CVD技术是建立在化学反应基础上的,既然是一种化学反应过程,就必须满足进行化学反应的热力学和动力学条件,而且要符合CVD技术本身的特定要求。
①必须达到足够的沉积温度,各种涂层材料的沉积温度,可以通过热力学计算得到。
②在沉积温度下,参加反应的各种物质必须有足够的蒸气压,如果反应物在室温下全部为气态,则沉积装置比较简单;如果反应物在室温下挥发较小,则需要加热使其挥发,同时还需运载气体将其带入反应室。
③产物中除了所需的硬质涂层材料为固态外,其余必须为气态。在沉积温度下,沉积物和基本材料本身的蒸气压要足够低,这样才能保证在整个反应过程中,反应生成的固态沉积物能很好地与基体表面相结合。
2.3.1.4 化学反应沉积热力学分析
要沉积所需要的涂层,可供选择的反应很多,那么选择什么样的反应最为合适呢?人们首先应用物理化学基本知识,对沉积过程进行热力学分析,找出反应向沉积涂层方向进行的条件以及平时能达到的最大产量或转换效率。如反应:A(g) C(g)+D(s), 要想沉积D,上述反应的lgKP应是较大的正值, 但要想D溶解进入气相, 即在原料区, 则lgKP应是较大的负值。lgKP与通常热力学数据表能查到的ΔG、ΔH、ΔS有以下关系:
(2-37)
式中 ΔG——标准状态下反应吉布斯自由能的变化;
ΔH,ΔS——标准状态下,反应的焓和熵的变化;
KP——反应的平衡常数。
上述反应的KP可表示为:
(2-38)
αD是固体活度(沉积物为纯物质时,一般为1),pA和pC分别为气体物质A和C的分压。
通常希望输入的气体物质A,能大部分转变成固体涂层D。若上述反应发生在密闭体系中,通入1atm(1atm=101.325kPa)的A,而且需要99%的A转换成C和D, 这时达到平衡, 应是0.01atm的A和0.99atm的C。A的转换效率为99%,需要的lgKP值应为:
(2-39)
lgKP继续增大时, 转换效率增加得并不多。表2-7为输入1atmA,增加A的转换百分数所需要的lgKP值。
从表2-7中可以看出,当lgKP值位于+1和+4之间时,A基本上完全转换成C和D。
表2-7 反应A(g) C(g)+D(s)的转换百分数与平衡常数的关系

对于不同的反应,用lgKP对1/T作图,从lgKP与ΔH和ΔS的关系式可以看出,直线的斜率应为-ΔH/2.303R,截距为ΔS/2.303R。 图2-20所示为假设的反应Ⅰ~Ⅴ的lgKP对1/T的曲线,可以用它来说明如何根据lgKP值选择传输-沉积反应。
从图2-20中可以看出,最佳的原料区条件应该是高于上虚线的部位,因为此处lgKP≤-3,而沉积区应在低于下虚线的部位, 此处的lgKP≥+3。反应Ⅰ是一个理性的从热到冷的或放热的传输-沉积反应,其中ΔH=-88kcal(1kcal≈4.2kJ), 原料区的温度应该控制在950~1100K范围内,而沉积反应应该控制在750~850K。反应Ⅱ具有较大的斜率(ΔH=-176kcal), lgKP一直到2000K左右还没有通过原料的范围, 这个反应由于温度太高而不宜使用, 因为选择容器有困难。反应Ⅲ的斜率又太小了(ΔH=-6kJ),但还可以采用。反应Ⅳ是一个很好的传输反应,但原料区和沉积区的温度正好和反应Ⅰ相反,它是一个从冷到热的传输反应,即沉积区的温度高于原料区,反应Ⅳ的沉积过程是吸热的(ΔH=+88kcal)。反应Ⅴ和反应Ⅰ的ΔH相等,它所处的原料区和沉积区温度较低,在这种情况下,不是得不到满意的沉积层,就是反应速率太慢,也可能由于温度低,传输物之一的蒸气压很低,所以它可能冷凝下来,妨碍反应的进行。

图2-20 假设的反应Ⅰ~Ⅴ的lgKP对1/T的曲线
通常来讲,密闭体系气相生长是比较缓慢的过程,它取决于气体的扩散和对流,它的总速率反比于原料端和沉积端之间的距离。
对于开放体系,选择反应所受到的限制要比密闭体系少,这是因为:非可逆和易可逆反应都可以使用;因为系统是开放的,生成的产物可以随时除去,这就改变了对lgKP值的要求。图2-21所示为几种不同型式的开放反应器,能够克服存在的热力学或动力学限制。所以如果对沉积总速率要求不是很高,不太合适的反应也可以采用。

图2-21 几种型式的开放反应器
使用不同类型的开放反应器,有以下几方面的考虑:①在原料区,如果反应物是在平衡条件下混合在一起的,如图2-21(c)所示,用lgKP曲线来选择反应与密闭体系是相似的;②如果反应物除了在高温的沉积区以外是不反应的[见图2-21(a)]或进入沉积区之前, 反应物不混合[见图2-21(b)和图2-21(d)]; 那么除了沉积区以外, 对lgKP不再有什么要求; ③如果反应物在进入沉积区之前不混合[见图2-21(d)], 那么在系统中, 每一个原料反应的lgKP值应按图2-21中对原料区的要求确定。由此可以看出,开放体系两个最主要的优点是沉积反应的热力学需要的条件放宽了,有的原料可装在气瓶中,这就提供了广泛的选择反应物或反应条件的可能性。
2.3.1.5 化学气相沉积反应物质源
确定涂层材料和CVD反应类型后, 最重要的问题就是选择参与反应的物质源。常用的物质源有以下几种。
(1)气态物质源
气态物质源是指在室温下呈气态的物质,如H2、N2、CH4、O2、SiH4等。这种物质源对CVD工艺技术最为方便。因为它只用流量计就能控制反应气体流量,而不需要控制温度。这就使涂层设备系统大为简化,对获得高质量涂层成分和组织十分有利。
(2)液态物质源
在室温下呈液态的反应物质称为液态物质源。这类物质源也分为两种:一种是该液态物质的蒸气压即使在相当高的温度下也很低,必须加入另一种物质与之反应,生成气态物质送入沉积室,参与沉积反应;而另一种液态物质源在室温或稍高一点的温度下,就能得到较高的蒸气压,满足沉积工艺技术的要求。这种液态物质源很多,如TiCl4、CH3CN、SiCl4、VCl4、BCl4等。控制液态物质源进入沉积室的量,一般采用控制载气和加热温度,当载气(如H2、Ar等)通过被加热的物质源时,就会携带一定数量这种物质的饱和蒸气。
载气携带物质的量,可由该液体在不同温度下的饱和蒸气压数据或蒸气压随温度变化的曲线,定量地估算出单位时间内进入反应室的蒸气量n,其单位为: mol/min。
n=102RTF/RT (2-40)
式中 RT——液体饱和蒸气压,以atm表示;
F——载气流量,L/min;
T——热力学温度,K;
R——摩尔气体常数,J/(mol·K)。
要想准确地控制物质源蒸气量, 达到反应气体分压的要求, 就必须严格、稳定控制载气流量和加热温度。但在实际应用时,还应该注意以下两个问题:一是文献中给出的蒸气压测定数值的测定条件和实际使用条件往往不尽相同(如气压沉积),不根据具体条件使用这些数据会造成较大的误差;二是盛装液体物质源的容器的大小和形状,也会影响携带蒸气量的多少。所以,为了精确控制反应物质,应按具体条件经试验测定出不同温度和不同载气流量下,每种液态物质源的蒸气量,确保满足沉积工艺要求。
(3)固态物质源
固态物质源,如AlCl3、NbCl3、TaCl5、ZrCl4等。它们在比较高的温度下(几百摄氏度),才能升华出需要的蒸气量,可用载气带入沉积室中。因为固体物质源的蒸气压在温度变化时,一般都很敏感(呈指数关系),因此对加热温度和载气量的控制精度更加严格,这对涂层设备设计、制造提出了更高的要求。
通常情况下,为了准确控制固态物质源的流量,采用HCl气体和纯金属发生气-固相反应,直接生成气态反应物质,再用载气输送到反应室内。如:
(2-41)
(2-42)
2.3.1.6 化学气相沉积影响因素
(1)化学反应
对于同一种沉积材料,采用不同的沉积反应,其沉积质量是不一样的。这主要来自两方面的影响:一是沉积反应不同引起沉积速率的变化,沉积速率的变化又影响相关的扩散过程和成膜过程,从而改变薄膜的结构;二是沉积反应往往伴随着一系列的掺杂副反应,反应不同导致薄膜组分不同,从而影响沉积质量。
(2)沉积温度
沉积温度是影响涂层质量的重要因素, 而每种涂层材料都有自己最佳的沉积温度范围。一般来说,温度越高,CVD化学反应速率也越快,气体分子或原子在基体表面吸附和扩散作用加强,故沉积速率也越快, 此时涂层致密性好,结晶完美。但过高的沉积温度,也会造成晶粒粗大的现象。当然沉积温度过低,会使反应不完全,产生不稳定结构和中间产物,涂层和基体的结合强度大幅度下降。
(3)沉积室压力
沉积室压力与化学反应过程密切相关。压力会影响沉积室内热量、质量及动量传输,因此影响沉积速率、涂层质量和涂层厚度的均匀性。在常压水平反应室内,气体流动状态可以认为是层流;而在负压立式反应室内,由于气体扩散增强,反应生成的废气能尽快排出,可获得组织致密、质量好的涂层,更适合大批量生产。
(4)反应气体分压
反应气体分压是决定涂层质量的重要因素之一,它直接影响涂层成核、生成、沉积速率、组成结构和成分。对于沉积碳化物、氮化物涂层,通入金属卤化物的量(如TiCl4), 应适当高于化学当量计算值, 这对获得高质量涂层是很重要的。
(5)衬底
化学气相沉积通常是在衬底表面进行的,因此衬底对沉积质量的影响也是一个关键因素。这种影响主要表现在:①衬底表面的附着物和机械损伤会使外延层取向无序而造成严重的宏观缺陷;②衬底界面的取向不仅影响沉积速率,也严重影响外延沉积的质量;③衬底与外延层的结晶学取向和沉积层的位错密度密切相关。
(6)气体流动状况
在化学气相沉积中,气体流动是质量输运最主要的表现形式,因此,气体流动状况决定输运速度,进而影响整个沉积过程。边界层的宽度与流速的平方根成反比,气体流速越大,气体越容易越过边界层到达衬底界面,界面反应速率越快。流速达到一定程度时,有可能使沉积过程由质量迁移控制转向表面控制,从而改变沉积层的结构,影响沉积质量。
2.3.1.7 化学气相沉积装置
采用CVD技术沉积涂层的材料种类和制备方法很多,因此CVD装置也有许多类型。负压CVD装置主要由以下几个部分组成:①反应气体流量控制;②金属卤化物(TiCl4、AlCl3等)蒸发制取及输送;③加热炉及温度控制;④沉积室及盛料舟;⑤沉积室压力控制;⑥真空及废气处理。
(1)原料气体配送及再净化系统
准确稳定地把各反应气体送入沉积室,对获得高质量涂层是非常重要的。测定气体流量过去多采用带针型调节阀门的玻璃转子流量计,而现在随着工业水平的发展,测定气体流量又多采用质量流量计,这种流量计测量的控制精度高,又带计算机接口,很容易实现自动控制。
CVD工艺要求所用的各反应气体,包括H2、N2、Ar、CH4、CO2、HCl等纯度稳定控制在99.995%以上,微水、微氧含量在5×10-6μL/L以下。对于用量大的H2、N2、Ar气体,在现场还需配有二次净化设备,进行脱水、脱氧,以确保原料气体纯度。表2-8所列为CVD工艺对反应原料种类及纯度的要求。
表2-8 CVD工艺对反应原料种类及纯度的要求

对于金属卤化物及含C、N有机化合物蒸发、制取及输送系统,严格控制输送到沉积室里的金属卤化物及CH3CN的气体分压,对采用CVD技术获得高质量硬质涂层材料是至关重要的。在实际生产中,大多是通过金属卤化物加热温度、载气量大小和输出压力的高低来控制金属卤化物及CH3CN的气体分压。金属卤化物的蒸发、升华温度差异很大。这在设计CVD设备系统时,应充分予以考虑。为了提高Al2O3硬质涂层材料的使用性能,获得高纯度无水AlCl3,在整个沉积工艺过程中,有效控制AlCl3气体分压是十分必要的。通常在现场采用高纯HCl和高纯Al,在400~500℃温度下反应制取高纯AlCl3, 并直接送入沉积室内,参与沉积反应,生成Al2O3涂层。这种方法和用AlCl3试剂加热升华的方法相比,AlCl3具有纯度高、流量易控制等优点,实际生产中应用广泛。
设计金属卤化物及CH3CN蒸发,制取及输送系统的关键是温度、压力和载气量的控制精度及稳定性、可靠性,否则很难保证金属卤化物及CH3CN气体分压始终处于恒定可控的状态。
(2)加热方式及控制系统
CVD装置的加热方式有电阻加热、高频感应加热,红外线和激光加热等,这应根据装置结构、涂层种类和反应方式进行选择。对大型生产设备而言多采用电阻加热方式。
生产中一般采用钟罩式内绕电阻丝加热炉,炉膛尺寸可按沉积室大小而定。为了保证有足够的有效恒温区,加热炉可按大小分多段进行独立加热,独立控温。各段测温、控温用铂铑-铂热电偶,沿炉子径向插到炉膛边缘上,加热电阻丝常采用铁铬铝电阻丝绕成,功率大小按要求计算。
加热炉最高使用温度为1100℃,常用使用温度在1050℃,炉壳温升不大于80℃。为了满足加热炉经常升、降、移位在不同位置加热工件,所有热电偶补偿导线和供电线路,通过特殊插头自动断开和连接,这样既方便又安全。
温度控制系统分加热炉、金属卤化物及CH3CN蒸发、制取及管路输出三部分。均采用PID智能数字温度调节仪表测温及控制,并有计算机接口,温度控制精度可达±(0.5~2)℃。
(3)沉积室及结构
在设计沉积室时,首先要考虑沉积室的形式(如立式、卧式等)、制造沉积室的材料、沉积室有效容积和盛料混气结构。
一个好的沉积室结构,应在保证产量的同时,还要做到:①各组分气体在沉积室内均匀混合;②要保证各个基体物件都能得到充足的反应气体;③生成附加产物能迅速离开基体工件表面,这样就能使每一件基体和同一件基体的各个部分,涂层厚度均匀一致,涂层质量性能均匀一致。
(4)排气系统
CVD装置大多会产生腐蚀性、有毒性废气和粉状副产物。这会对真空泵和环境造成很大损害,所以在大批量生产中,真空机组多用水喷射泵和液体循环真空泵,废气采用冷阱吸收和碱液中和等手段,去除酸气和有害粉尘,使尾气排放达到环保要求。
排气系统是CVD装置在安全方面最为重要的部分,该系统具有两个主要功能:一是从反应室除去未反应的气体和副产物:二是提供一条反应物越过反应区的通畅路径。其中未反应的气体可能在排气系统中继续反应而形成固体粒子。由于这些固体粒子的聚集可能阻塞排气系统而导致反应器压力的突变,进而形成固体粒子的反扩散,影响涂层的生长质量和均匀性,因此,排气系统的设计应充分予以注意。
2.3.2 低压化学气相沉积(LPCVD)
从本质上讲,低压化学气相沉积(约10kPa)是相对于常压化学气相沉积而言的。由于反应器工作压力的降低大大增强了反应气体的质量输送速度,从而使低压化学气相沉积呈现出新的特点,因此,低压化学气相沉积在半导体工艺中得到广泛的应用。
在常压下,质量迁移速度与表面反应速率通常是以相同的数量级增加的。而在低压下,质量迁移速度的增加远比界面反应速率快。反应气体穿过边界层,当工作压力从1.0×105Pa 降至70~130Pa时,扩散系数增加约1000倍。因此,在低压化学气相沉积中,界面反应是速度控制步骤。由此判断:低压CVD在一般情况下能够提供更好的膜厚均匀性、阶梯覆盖性和结构完整性。
图2-22为典型的半导体工业涂覆硅晶片用低压化学气相沉积装置。该反应系统采用卧式反应器,具有较高的生产能力。它的基座水平放置在热壁炉内,可以非常精确地控制反应温度,减轻设备的复杂程度;另外,它采用垂直密集装片方式,进一步提高了系统的生产效率。采用正硅酸乙酯沉积二氧化硅薄膜时,与常压CVD相比,LPCVD的生产成本仅为原来的1/5,甚至更小,而产量提高了10~20倍,沉积薄膜的均匀性也从常压的±8%~±11%提高到±1%~±2%。

图2-22 典型的半导体工业涂覆硅晶片用低压化学气相沉积装置
2.3.3 激光辅助化学气相沉积
激光辅助气相沉积是采用激光能量激活CVD化学反应从而使常规CVD工艺得到强化的技术。从强化反应的角度来看,LCVD与PECVD类似,然而这两种技术之间有一些重要差别,例如等离子体中,电子的能量分布比激光发射时的光子的能量分布要宽得多。比较这两种技术可以看出LCVD具有某些优点(见表2-9)。其中LCVD 又可分为热解LCVD和光解LCVD两类。
表2-9 LCVD和PECVD的比较

(1)热解LCVD
激光热解在激光能量接触并加热吸附反应气体的衬底时发生。这时必须选择这样的激光波长,使气体分子对激光的能量吸收很少或根本不吸收能量,而衬底对激光的吸收系数较高。因为激光对衬底的加热属于局部加热,所以沉积仅局限于加热区域。图2-23为激光束直线穿过衬底沉积细条纹的示意图。

图2-23 激光束直线穿过衬底沉积细条纹的示意图
(2)光解LCVD
激光光解反应由光的作用,特别是紫外线来诱发,该激光具有足够的光能打断反应分子的化学键。在大多数情况下,这些分子具有宽频电子吸收带,而且很容易被紫外辐射所激发。光化学反应也可以用紫外灯发出的光线激发,但采用紫外激光器能够得到强度更强、单色性更好的紫外辐射。准分子激光器是普遍采用的紫外激光器,可以提供的光子能量为3.4~6.4eV,典型的光解LCVD装置如图2-24所示。

图2-24 典型的光解LCVD装置
1—反应气体;2—窗口;3—光栏;4—衰减器;5—加热器;6—窗口;7—加热器;8—气体副产物排放喷嘴
光解LCVD和热解LCVD的不同之处在于:光解LCVD一般不需要加热,因为反应是光激活的沉积,有可能在室温下进行。另外,对所使用的沉底类型也没有限制,透明的、不透明的、有吸附能力的,甚至对温度敏感的都没关系。但光解LCVD的一个致命弱点是沉积速率太慢,这大大限制了它的应用。如果能够开发出大功率的准分子激光器,那么光解LCVD完全可以和加热CVD及热解LCVD相竞争。特别是在许多关键的半导体加工方面,降低沉积温度是至关重要的,具有以下特点。
利用激光的单色性可以选择性地发生光化学反应,并可降低沉积薄膜的温度,防止或减小基片变形及减少来自基片的膜层掺杂;激光的聚束性好,能量密度高,且可实现微区沉积;激光束具有良好的空间分辨率和二维可控性,能够对集成电路进行局部修补或局部掺杂。结合计算机技术,可以沉积完整的薄膜图形,直接制作大规模集成电路;激光CVD的主要缺点是装置复杂,价格昂贵,尤其在沉积大面积薄膜时需要配置激光扫描装置。
LCVD和一般CVD法不同,CVD法是使整个基片上都产生沉积层,而LCVD法是用激光束仅对基片上需要沉积的部位照射光线,结果只在基片的局部形成沉积层。LCVD加热为局部化,所以局部温度很高。LCVD中可以对反应气体预热,其浓度可以较高,来自基片以外的污染很小。对于形核,表面缺陷不仅可起到成核中心的作用,而且也起到强吸附作用,因此激光加热时会产生较高的温度。激光器的强度和辐射时间对沉积薄膜的厚度有很大影响,薄膜的厚度可以控制在小于10nm,也可大于20μm。沉积膜的直径与辐射条件有关,最小的可以控制到激光束直径的1/10,这样就避免了因大面积加热而引起基体性质的变化。基材温度的大大降低,可在不承受高温的基材上合成薄膜。例如:用LCVD制备SiO2、Si3N4、AlN薄膜时基材需要加热到380~450℃。
LCVD技术是近年来迅速发展起来的先进表面沉积技术,可广泛应用于微电子工业、化工、能源、航空航天以及机械工业。应用LCVD技术,人们已经获得了Al、Ni、Au、Si、SiC、多晶硅和Al/Au膜。
尽管激光光解CVD目前还停留在实验上,但近年来,已开始进入用准分子激光进行激光光解沉积的活跃期,已从准分子激光沉积金属及α-Si∶H,如使用SiH4∶Ar混合气,在基体温度为200℃时,可沉积出具有平行结构的质量优良的α-Si∶H膜层。现在已开始进行了用准分子激光器低温沉积金刚石膜和类金刚石膜的探索及微细加工的研究,而且在低温沉积金刚石膜方面取得了进展。
用LCVD技术制造的Si3N4,光纤传输微透镜已开始在工业上应用。其衬底材料选用石英,反应气体用SiH4-NH3,辅助气体为N2,沉积膜厚度根据工艺可控制在0.2~40μm,膜层的平均硬度HK为2200,最高可达3700;Si3N4沉积膜层的耐磨性能比基材提高了9倍之多;沉积Si3N4薄膜的基材在H2SO4溶液中的抗蚀性能大大提高。
2.3.4 有机金属化学气相沉积
有机金属化学气相沉积(MOCVD)是一种利用有机金属化合物的热分解反应进行气相外延生长薄膜的CVD技术。简单而言:载气把金属有机化合物和其他气源携带到反应室中加热的衬底上方,随着温度的升高在气相和气-固界面发生一系列化学变化和物理变化,最终在衬底表面上生成外延层。从1968年Rockwell公司的Manacevit提出第一篇MOCVD技术报告后,经过30多年的发展,MOCVD技术已逐渐变成了半导体生长的一种关键技术,它较其他外延技术具有更多优点,尤其适合于大规模工业化生产,使其成为实际应用中最广泛的外延技术,目前主要用于化合物半导体薄膜的气相生长。
2.3.4.1 原理
MOCVD法中用作原料的化合物必须满足以下条件:①在常温下稳定且容易处理;②反应的副产物不应妨碍晶体生长,不应污染生长层;③为适应气相生长,在室温附近应具有适当的蒸气压(>100Pa)。
通常可选用金属的烷基或芳基衍生物、羟基衍生物、羰基化合物等为原材料,元素周期表中的Ⅲ~Ⅴ族、Ⅱ~Ⅳ族化合物的构成元素,同属于周期表中B族的部分元素。其粗线左侧元素具有较强的金属性,不能构成满足要求的无机化合物原料,但其有机化合物特别是烷基化合物大多能满足作为原料的要求。右侧元素具有较强的非金属性,其氢化物能满足MOCVD的原料化合物要求。此外,不仅金属烷基化合物,而且非金属烷基化合物都能作为MOCVD原料,因此可用作原料化合物的物质相当多。例如:对GaAs、Ga1-xAlxAs作为Ga、Al的原料可选择(CH3)3Ga(三甲基镓TMG)、(CH3)3Al(三甲基铝TMA); 有时也使用三乙烷基镓(TEC)和三乙烷基铝(TEA)。p型掺杂源使用充入到不锈钢发泡器中的二乙烷基锌(DEZ)。作为As原料可选择AsH3气体。使用以上原料,在高温时使其发生热分解就可得到化合物半导体,典型装置如图2-25所示,发生的反应如下:
(2-43)
(2-44)
因为在气态下发生的反应会阻碍外延生长,所以需要控制气流的速度,以便不在气相状态下发生反应。反应的生成物从反应室下部排出,以消除废弃的影响。从图2-25中可以看出MOCVD设备主要包括高纯载气处理系统、气体流量控制系统、反应室、温度控制室、压力控制系统和尾气处理系统等。大多数半导体对纯度的要求较为严格,必须采用精密的设备、极其纯净的气体和安全的尾气处理系统。

图2-25 MOCVD示意图
1—提纯装置;2—流量计;3—TEC;4—TMA;5—DEZ;6—AsH3+H2;7—H2Se+H2;8—GaAs基片;9—射频线圈;10—石墨架
对于MOCVD法生长半导体薄膜的动力学模型大多认为是复相化学反应机构,由于在衬底上面存在着边界层,所以认为其生长过程是按下列步骤进行的。
①反应物从其在反应室的出口到反应衬底的输运。
②反应物通过扩散,穿过边界层到达衬底表面。
③反应物分子吸附在高温衬底表面上。
④吸附分子间或吸附物与气体分子间发生化学反应所生成生长晶体的原子和气体副产物。
⑤生成的生长晶体的原子沿衬底表面扩散,到达衬底表面上晶格的某些折角或台阶处结合进入晶体点阵中。
⑥副产物从表面解吸扩散穿过边界层进入主气流中被排出系统。
2.3.4.2 特点
在外延技术中,外延生长温度最高的是液相外延生长法,分子束外延方法的生长温度最低,而有机金属化学气相沉积法居中,它的生长温度接近于分子束外延。从生长速率上看,液相外延方法的生长速率最快,而有机金属化学气相沉积方法次之,分子束外延方法最慢。在所获得的纯度方面,以液相外延法生长膜的纯度最高,金属有机化学气相沉积和分子束外延方法生长的膜次之。总之,有机金属化学气相沉积法的特点介于液相外延生长法和分子束外延生长法之间。
MOCVD是近十几年迅速发展起来的新型外延技术,成功地用于制备超晶格结构、超高速器件和量子阱激光器等。MOCVD之所以得到迅速发展,主要是其独特优点所决定的。
(1)MOCVD的优点
①沉积温度低。例如ZnSe薄膜,采用普通CVD技术沉积温度在850℃左右,而MOCVD仅为350℃左右;由于沉积温度低,因而减少了自污染,提高了薄膜的纯度;许多宽禁带材料有易挥发组分,高温生长易产生空位,形成无辐射跃迁中心,且空位与杂质存在是造成自补偿的原因,所以低温沉积有利于降低空位密度和解决自补偿问题,对衬底的取向要求低。
②由于不采用卤化物原料,因而在沉积过程中不存在刻蚀反应,以及可通过稀释载气来控制沉积速率等,有利于沉积沿膜厚度方向成分变化极大的膜层和多次沉积不同成分的极薄膜层,因而可用来制备超晶格材料和外延生长各种异质结构。
③适用范围广,几乎可以生成所有化合物和合金半导体。如控制Ⅲ族Al、Ga、In等有机金属的物质的量的比,可以生成不同成分的混合晶体。而且MOCVD是非平衡的生长过程,能沉积卤族CVD和液相外延(LPE)不能制取的混合晶体。
④反应装置容易设置,较气相外相简单。生长温度范围较宽,生长易于控制,适宜于大批量生产,可在蓝宝石、尖晶石基片上实现外延生长。
(2)MOCVD的缺点
①虽然采用有机金属化合物取代普通CVD中常见的卤化物,消除了卤化物的污染和腐蚀性带来的危害,但许多有机金属化合物有毒和易燃,给有机金属化合物的制备、储存、运输和使用带来了困难,必须采用严格的保护措施。
②由于反应温度低,有些金属有机化合物在气相中就会发生反应,生成固态颗粒再沉积到衬底表面,形成薄膜中的杂质颗粒,破坏了膜的完整性。
以上这些步骤是按顺序进行的。由于每一步的速率是不相同的,因此总的生长速率由其中最慢的一步来决定,这最慢的一步叫速率控制步骤。一般低温时为表面反应控制过程或动力学控制过程,高温时为质量控制过程。
2.3.4.3 MOCVD的应用
MOCVD技术日益受到人们的广泛重视,MOCVD法可以沉积各种金属以及金属氧化物、碳化物、氮化物和硅化物膜层,可以制备GaAs、GaAlAs、InP等最通用的化合物半导体。然而MOCVD所用的设备及金属有机化合物都十分昂贵。因此,只有当要求获得很高质量的外延膜层时,才考虑采用MOCVD方法。MOCVD法具体有以下几个方面的应用。
①化合物半导体材料。MOCVD技术的开发和发展主要是针对半导体材料外延沉积的需要。
②各种涂层材料。包括各种金属、氧化物、氮化物等涂层材料。沉积这类材料可以采用常规CVD法,但金属氯化物在高温条件下比较稳定,而衬底材料又不能承受CVD反应所需的高温,为此,采用MOCVD法可在较低工艺温度下制备这些涂层材料。
③光器件。用MOCVD法制作的激光器,在临界电流值上与其他方法制作的没有差别。在使用上,MOCVD法制作的Ga1-xAlxAs系激光器的寿命接近唯一得到实用的LPE激光器的寿命。在长波宽带激光器技术上也有进步。运用MOCVD技术可精确地控制薄膜的组成和厚度,用MOCVD技术可制备多量子阱激光器。另外,也有利用MOCVD法制作的Ga1-xAs/GaAs系太阳能电池的应用实例,其转换效率为23%,具有LPE法制备太阳能电池的最佳性能。
④电子器件。MOCVD制作的膜只限于具有高迁移率的化合物半导体n型GaAs,这类电子器件要求的外延生长层的载流子浓度与膜厚度需要精确控制,如GaAs的电子器件,膜厚需要在两个数量级内,而电子浓度要在四个数量级内进行控制,MOCVD法均可在这一范围内满足要求。
由此可以看出,MOCVD法要比一般的CVD法更具有应用的广泛性、通用性和先进性。在现代表面技术中,随微电子工业的发展和要求,一定会取得更大的突破。
2.3.5 等离子体增强化学气相沉积
等离子体增强化学气相沉积(plasma enhanced chemical vapor deposition,PECVD)又称等离子体辅助CVD, 它是在传统CVD基础上发展起来的一种新的制膜技术,特别适用于功能材料薄膜和化合物薄膜的合成,并显示出一定的优势。相对于真空蒸镀和溅射而言,被视为第二代薄膜技术。
经常使用的等离子体有直流等离子体、射频等离子体和微波等离子体等。需要说明的是,PECVD中的化学反应过程比较复杂,沉积薄膜的性质与沉积条件密切相关,影响膜层质量的因素较多,而且因素之间的互相干扰,导致难以控制,其反应机理、反应动力学、反应过程目前不十分明确。表2-10列出了PECVD法制备薄膜的一些典型例子。
表2-10 PECVD法制备薄膜的一些典型例子

2.3.5.1 等离子体增强化学气相沉积原理及装置
等离子体增强化学气相沉积技术采用气态物质源,工件接负高压电源,借助于外部电场的作用引起气体辉光放电,使前驱气体成为等离子状态,在等离子体电场中气体通过激发、离解、电离等过程变成高能量的气体离子,增强了反应物质的化学性质,促进了气体间的化学反应,从而在阴极-工件表面反应沉积为金属硬质涂层化合物或者薄膜。图2-26为直流脉冲PECVD设备简图。

图2-26 直流脉冲PECVD设备简图
1—加热炉;2—测温仪;3—直流脉冲电源;4—真空计;5—真空排气系统;6—工作台;7—沉积室
辉光放电是典型的自激发放电现象。这一放电最主要的特征是从阴极附近到克鲁克斯暗区的场强很大。在阴极辉光区中,会发生比较强烈的气体电离,同时发生阴极溅射,为沉积薄膜提供了清洁而活性高的表面。由于整个工件表面被辉光层均匀覆盖,使工件能得到均匀的加热。阴极的热能主要靠辉光放电中激发的中性粒子与阴极粒子碰撞所提供,一部分粒子轰击也是阴极能量的来源。辉光放电的存在,使反应气氛得到活化,其中基本的活性粒子是离子和原子团,它们通过气相中电子,分子的碰撞产生,或通过固体表面离子、电子、光子的碰撞所产生,因而整个沉积过程与只有热激活的过程有显著不同。以上这些作用在提高涂层的结合力、降低沉积温度、加快反应速率等方面都创造了有利的条件。
2.3.5.2 PECVD工艺过程
①安装工件。经清洗后的待处理工件,按要求摆放在沉积室,并接好电源。系统检漏后,通入H2恢复常压。
②加热工件。套上外加热电炉对沉积室进行加热。
③抽真空。工件温度升至规定温度后,启动真空泵对系统排气抽空。
④轰击净化或离子渗氮。 通入Ar或N2,通入直流脉冲电源对物件表面进行轰击净化或离子渗氮。
⑤按要求通入反应气体沉积涂层。
⑥沉积工序结束后,停止通入气体,冷却至室温,即可打开沉积室取出涂层。
2.3.5.3 PECVD的特点
(1)优点
①实现了薄膜沉积工艺的低温化。在常规CVD技术中需要用加热使初始气体分解,而在PECVD技术中利用等离子体中电子的动能去激发气相化学反应,故可在较低的温度下进行。许多在热CVD条件下不能进行的或者进行缓慢的反应能够得以进行。例如:对沉积硅外延膜时,采用热CVD法需要在1000~1250℃之间进行,而采用PECVD技术只需要在750℃左右即可进行,二者的对比情况见表2-11。
表2-11 PECVD技术与热CVD法的沉积温度范围

②PECVD技术大多在较低的压力下进行,可以提高沉积速率,增加膜厚均匀性,这是因为多数的PECVD在辉光放电中所用的压力比较低,从而增强了反应气体与生成气体产物穿过边界层,在平流层和衬底之间的质量输运;同时由于反应物中分子、原子等粒子团与电子之间的碰撞、散射、电离等作用,膜厚度的均匀性也得到了改善,膜层针孔小、组织致密、内应力小、不易产生微裂纹。
③可获得性能独特的薄膜。需要不断地从外界给PECVD系统输入能量,才能维持其稳定性,一些按照平衡理论不能发生的反应和不能获得的物质结构,在PECVD系统中可能发生。例如体积分数为1%的甲烷在H2中热解时,在热平衡的CVD中得到的是石墨薄膜,而在非平衡的等离子体化学气相沉积中可以得到金刚石薄膜。
④可以用于生长界面陡峭的多层结构。 在PECVD的低温沉积条件下,如果没有等离子体,沉积反应几乎不能发生。而一旦有等离子体存在,沉积反应就能以适当的速率进行。由于等离子体开始反应的时间相当于气体分子的碰撞时间,因此利用PECVD技术可生长界面陡峭的多层结构。图2-27为气相沉积法制备的α-C∶H∶Si∶O /α-C∶H 36层涂层的横断面。

图2-27 气相沉积法制备的α-C∶H∶Si∶O/α-C∶H 36层涂层的横断面
⑤可以提高沉积速率,增加膜层均匀性。因为在多数情况下,PECVD系统压力低,增强了前躯体和气态副产物穿过边界层在平流层和衬底表面之间的质量输运。
(2)缺点
①等离子体容易对衬底材料和薄膜造成离子轰击损伤。在PECVD过程中,相对于等离子电位而言,衬底电位通常较负,这势必造成等离子中正离子被电场加速后轰击衬底,导致衬底损伤和薄膜缺陷。
②因为沉积温度低,反应过程中产生的副产物气体和其他气体的解吸进行得不彻底,经常残留在膜层中,很难保证化合物的化学计量比,如用此法沉积DLC膜时,膜中存在着大量的氢,对膜的力学、电学、光学性能有很大影响。
③PECVD反应是非选择性的。等离子体中电子的能量分布范围很宽,除电子碰撞外,在离子碰撞作用和放电时产生的射线作用下也可产生新粒子,因此PECVD反应很可能同时存在几种化学反应,使反应产物含量低得控制困难。
④PECVD装置一般比较复杂,且价格昂贵。
2.3.5.4 PECVD的重要应用
①绝缘膜的PECVD沉积。在低温下沉积SiN等硅的化合物一类的绝缘膜,这对于超大规模集成芯片的生产是非常重要的。
②非晶和多晶硅薄膜的PECVD沉积。非晶硅是一种优良的半导体材料,用途较广,主要用在太阳能电池方面;多晶硅可用作金属氧化物半导体元件的栅极以及场效应管的发射极,也可用于集成电路的互联材料以及高度交联的网格结构材料,同时在反应过程中可引入新的基团或元素,实现功能设计。
③金刚石和类金刚石的PECVD沉积。自1983年Mjamo等开发的微波PECVD低压合成金刚石薄膜的方法取得了突破性的进展以来,金刚石的工业化生产便成为可能。
④等离子体聚合。由于等离子体聚合生成聚合物,因此,等离子体聚合技术日益引人注目,正越来越广泛地应用于开发有界电特性、导电特性、感光特性的离子体聚合膜和一些重要的有机金属复合材料。
⑤PECVD的典型应用之一是沉积微电子器件用绝缘膜,在低温下沉积氮化硅、氧化硅或硅的氮氧化物一类的绝缘膜,这对于超大规模集成生产是至关重要的。氮化硅具有优良的阻挡碱金属离子和湿气的能力,因而常用作集成电路的钝化膜。而作为多层布线和器件表面保护的氮化硅膜,一般要求厚度大于600nm,高温Si3N4膜还存在选择性腐蚀问题,使其应用受到限制。采用低压CVD沉积温度高,薄膜应力大,如果沉积厚度大于20μm,将会发生龟裂。而PECVD的一个重要优点是能够在温度较低的情况下沉积,大约为250~400℃,这样低的温度即使在采用铝作为布线材料的晶片上也足以沉积薄膜。PECVD沉积SiO2绝缘层被广泛地应用于半导体器件工艺,最近几年在光学纤维涂层和某些装饰性涂层方面获得了应用。